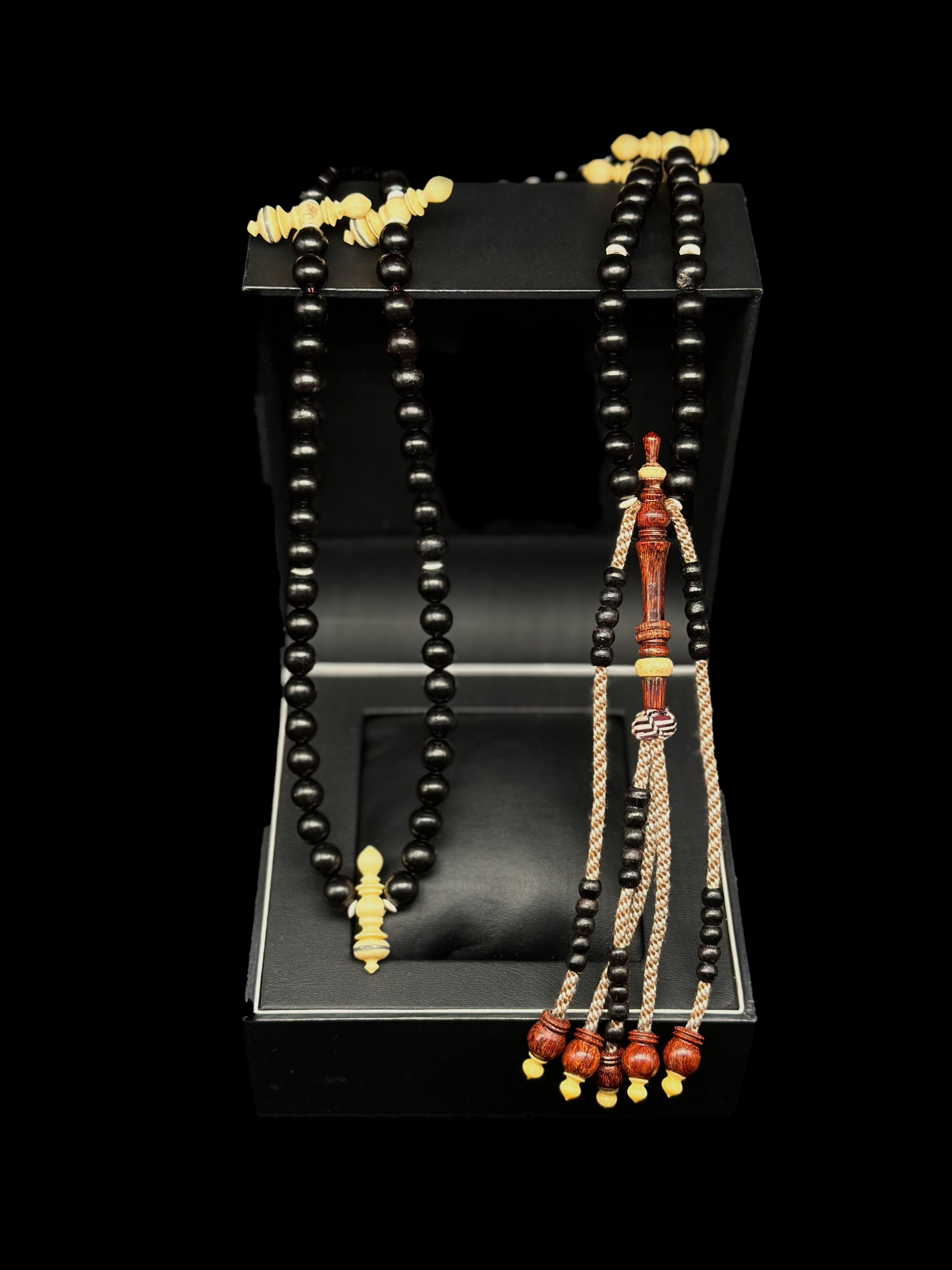
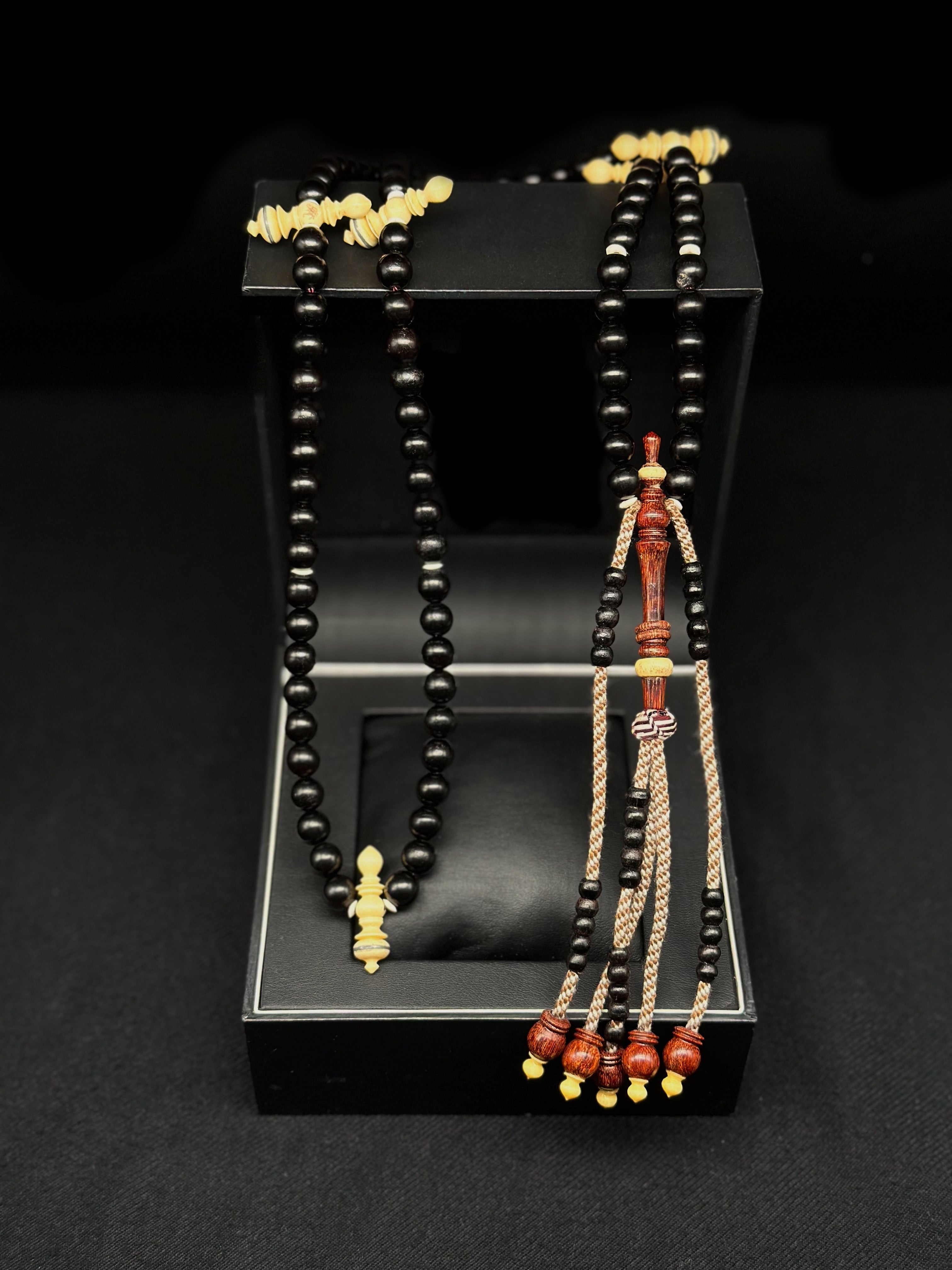
Ebony x Tamarind x Cow Bone Rumi Tasbih
The Material
Ebony, the million dollar wood.
Origin
Ebony wood is a dense, dark hardwood known for its deep black color, fine grain, and smooth finish. Harvested from trees in the genus Diospyros, ebony has been highly prized for centuries due to its durability, luxurious appearance, and rarity. The wood is incredibly dense, allowing it to sink in water and making it ideal for fine woodworking, musical instruments, and high-quality furniture.
History
he use of ebony dates back to ancient civilizations. In ancient Egypt, ebony was a symbol of luxury and was used to craft royal furniture, ceremonial objects, and inlays for ornate items. It was also a favored material for creating statues and carvings for pharaohs, believed to embody divine qualities due to its dark, mysterious appearance.
In Africa, particularly in Madagascar and West Africa, ebony has long been a material of cultural and spiritual importance. It has been carved into masks, tools, and sculptures, often representing power, wisdom, and protection.
During the Middle Ages, ebony was highly sought after by European royalty and nobility. It was imported through trade routes from Africa and Asia and used to create intricate pieces of furniture, chess sets, and religious icons. The rich black wood became a symbol of wealth and sophistication, further cementing its status as a prized material in global craftsmanship.
The Craft
Stage 1 – The Design:
The intricate design of the prayer beads are envisioned by the craftsman and a rough outline is sketched out onto a blank canvas. It is at this stage where the craftsman selects which materials they wish to utilise.
Stage 2 – Acquisition of the raw materials:
The hunt for the chosen materials begins and the wood is then ethically sourced and harvested from the finest and 100% organic of materials.
Stage 3 – The resize:
Once the material has been sourced it is then cut into smaller blanks and is now ready to begin onto the next stage of the process.
Stage 4 – The carving:
At this stage the beads, minarets, and separator pieces are carved into the desired shape and pattern. It is important to know that this entire method is done by hand; there are no molds, markers or guidelines. This is a skill and art form which requires exquisite hand co-ordination and takes a craftsman many years to learn and perfect.
Stage 5 – Excavating the holes:
Similar to the last stage this is a skill which requires years of practise. There are no markers or guidelines, and if the holes are off by even a fraction of a millimetre the prayer beads will not be aligned correctly. If the holes are too narrow this will result in the beads being stiff and difficult to move along the thread. If the holes are too wide this will result in the beads being extremely loose and difficult to use.
Stage 6 – Unmasking the natural beauty:
The materials are then sanded to bring out the beauty which is hidden deep within the beads. slowly each and every grain is uncovered and is manifested within each bead.
Stage 7 – The set up:
There are currently 3 main set up systems of how prayer beads are separated;
Shadhili – 100 beads separated using 3 dividers in the set up of 33/17/17/33.
Naqshbandi – 200 beads separated using 7 dividers in the set up of 7/11/40/70
Tijani – 100 beads separated using 5 dividers in the set up of 12/18/20.
Stage 8 – The stringing:
The beads are now finally ready to be stringed together using a durable thread. It is at this stage where the thread tension is decided on and with some can even be adjusted afterwards.
Stage 9 – The tassel:
This process takes hours to complete and is crucial in the overall look and design of the prayer beads.
Stage 10 – The inspection:
The set of prayer beads are now ready for one last inspection before they are to be released.
Specification
Bead Count: 100
Bead Size: 9.5mm
Material: Ebony
Choose options
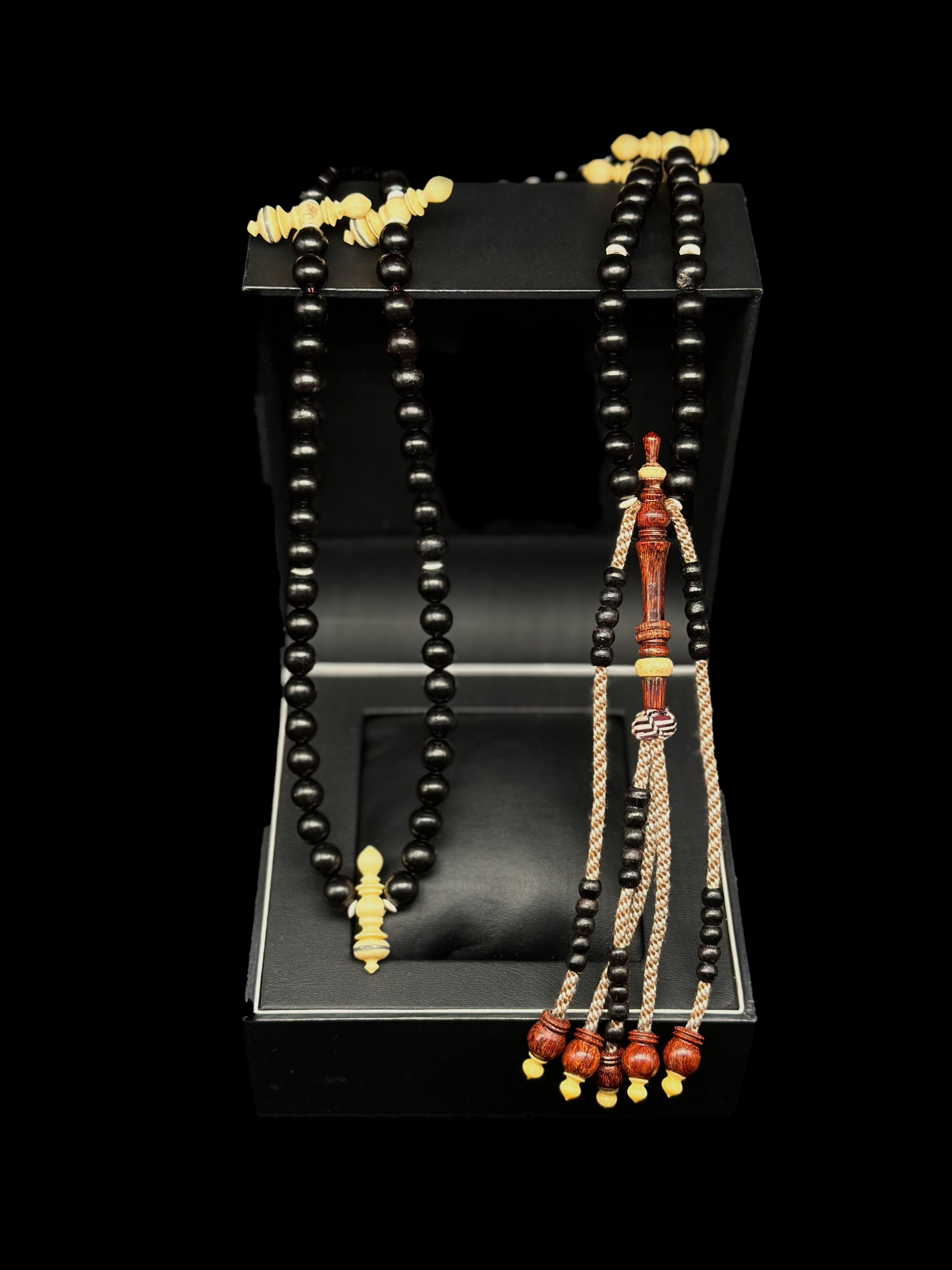
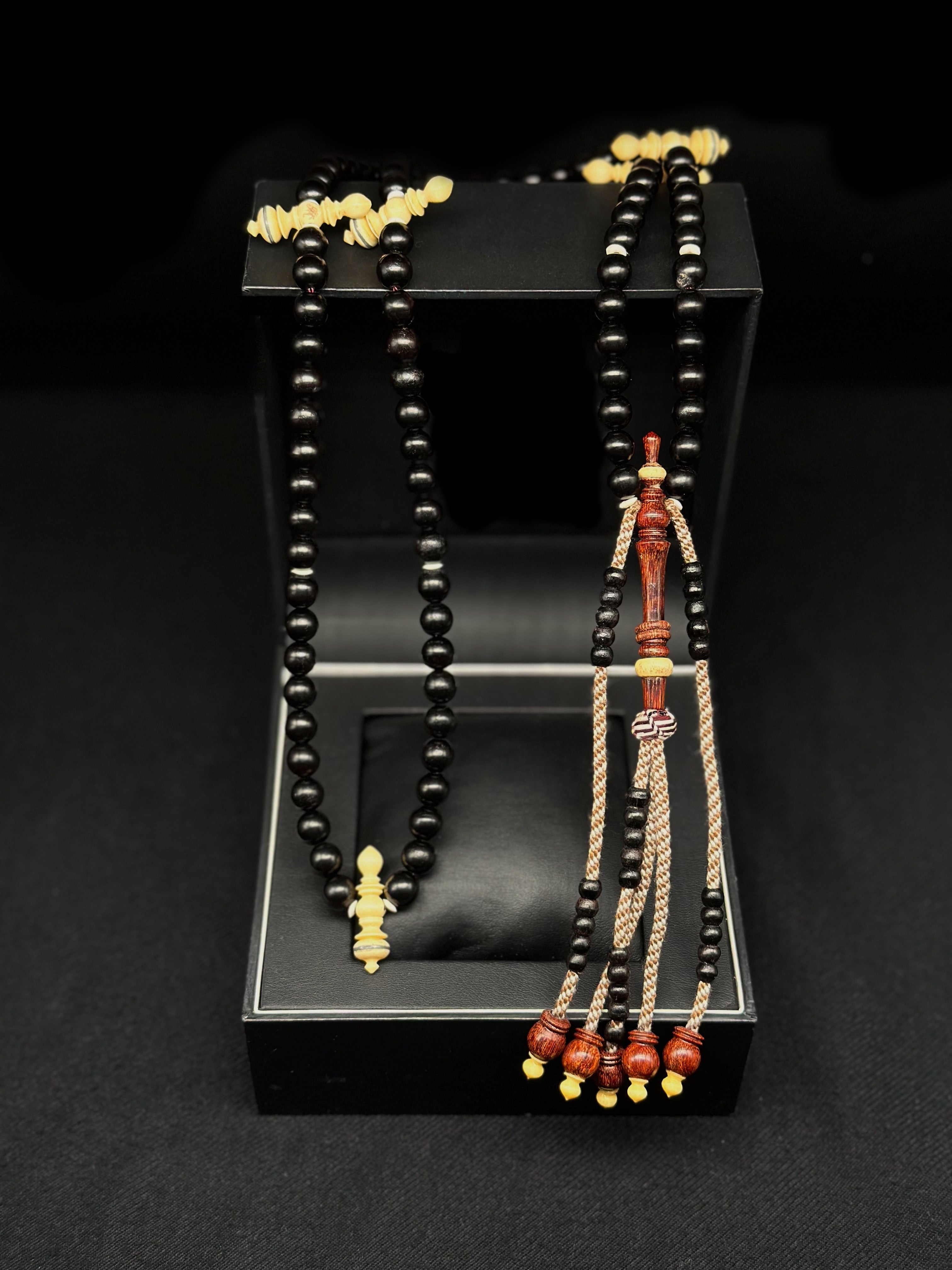